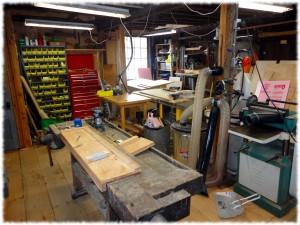
Yes, yes, I know what you are thinking. What about the mud room? Of course you must have done that last little push to completion before diving back into the workshop. Or, will the mud room fall to the bin of ADHD unfinished projects?
Well, no, the mud room isn’t finished. And yes, I know, all of us with ADHD have basements/workshops/houses filled with great intentions and unfinished projects. Heck, come to think of it, there is probably still a sixth-grade science fair project sitting in my lifelong unfinished projects bin. But I promise, the mud room won’t be put in that bin. Of course, saying I’ll finish a project and actually finishing it are two different things.
It is always easy to make an excuse for an unfinished project – so I’ll make one now – I’m waiting on the paint to dry on the last two window sashes. They should be dry by tomorrow, so hopefully by this weekend I’ll be able to finish that window (and for the most part, the mud room) and post that to the blog.
But back to the workshop. I recently added a thermostat for the kerosene heater, and have started adding insulation so the heater would actually head the space to a usable temperature. I spent several evenings over the past week working on odds and ends projects in the workshop and the house.
In the shop I cleaned up most of the mess that had accumulated through a fall house renovation project. I also decided to move the workbench away from the wall – I think it may be useful to be able to access the back side of the bench while I’m working on a project. I’ll have to see how it works.
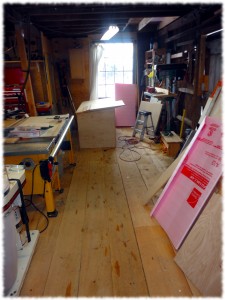
I also moved the dust collector back to the center of the shop, and moved the tablesaw and jointer over a little bit (to accommodate the dust collector). The bandsaw was moved to the corner where the dust collector had been, but it isn’t a great place for the bandsaw. I’ll still have to find a better home for that tool.
In addition to cleaning and improving insulation in the shop, I was able to get back to the toy box construction. The second box is nearly complete. I attached the top this week and glued up the door panels today. If the weather/heating supports finishing, I should be done with the second box by the end of this week.