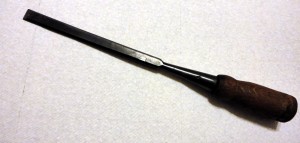
This morning the boys and I visited the local flea market. The boys were on a search for a new toy. I wasn’t looking for anything particular, but of course stopped by the tool vendors to see if anything caught my eye. For $5 I picked up a vintage 1/2-inch socket chisel. The blade was in very good shape, and the price was right. Tonight I decided to sharpen it. I figured I would document how I took an old flea market find and turned it into a sharp chisel. Not that I’m trying to tell anyone else how to do it, but I figured it would be interesting to look back in a few years and see if what I did still makes sense. But maybe by then I’ll only purchase new chisels. Just not from the box store. $5 (if one doesn’t count the cost of the sharpening stones) and 15 minutes on the water stones and I have a much better chisel than any crap one can pick up at a box store.
First thing I did was take a close look at the blade to see how much metal I needed to take off. In this case the blade was in good shape (no pitting or nicks):
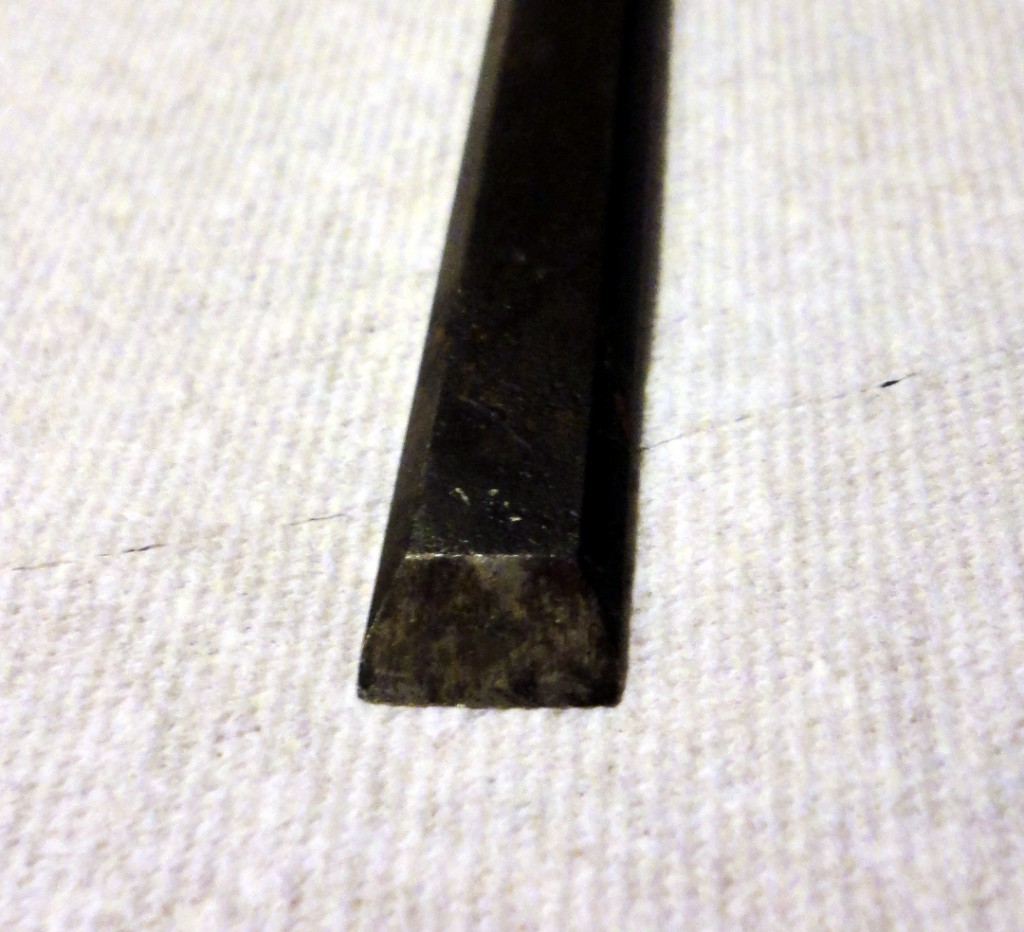
Next I get the waterstones ready. It is too cold to work out in the workshop this time of year, so I take over the kitchen:
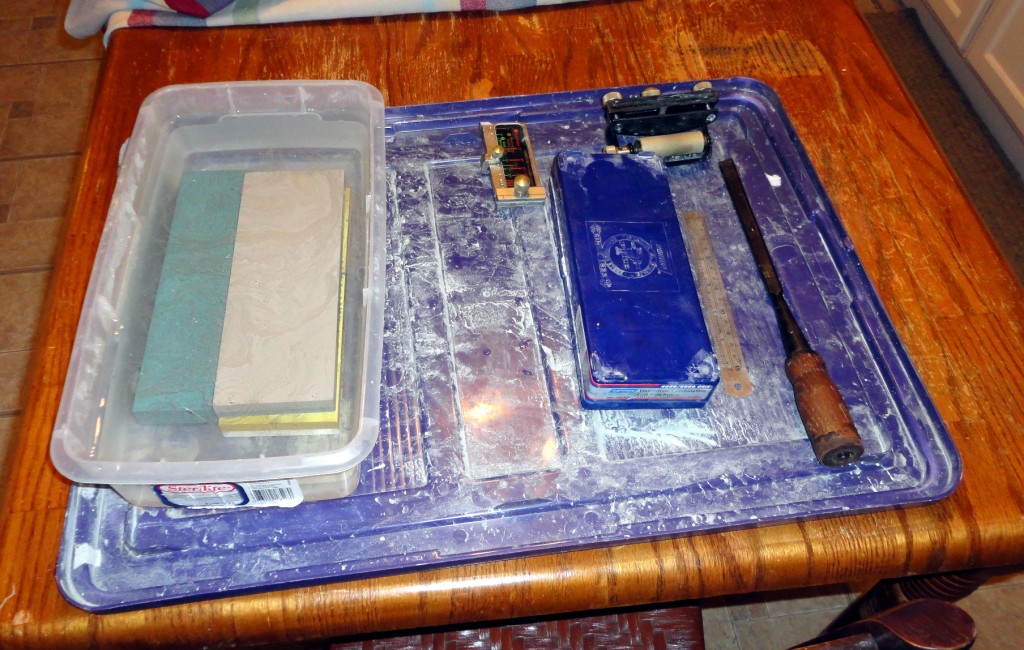
Next I flatten the back starting with the 220-grit and working my way to the 8000-grit stone. I use a thin ruler on the edge of the stone so I only have to flatten the back near the tip (it saves a lot of time flattening):
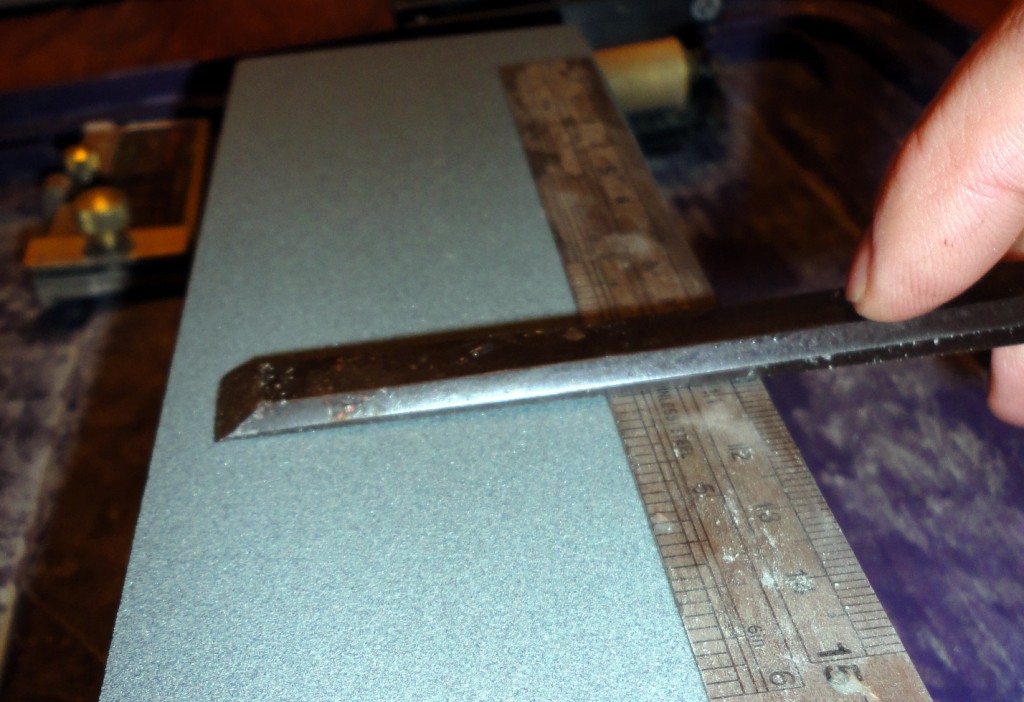
Next I put the chisel in my Veritas honing guide and work my way from the coarse to 8000 grit. I will periodically turn the chisel and flatten the back as I work (to get rid of the wire that forms when aggressively removing metal). For this chisel, the process took only 5 minutes to sharpen the bevel. I sharpened this with a 30-degree bevel angle:
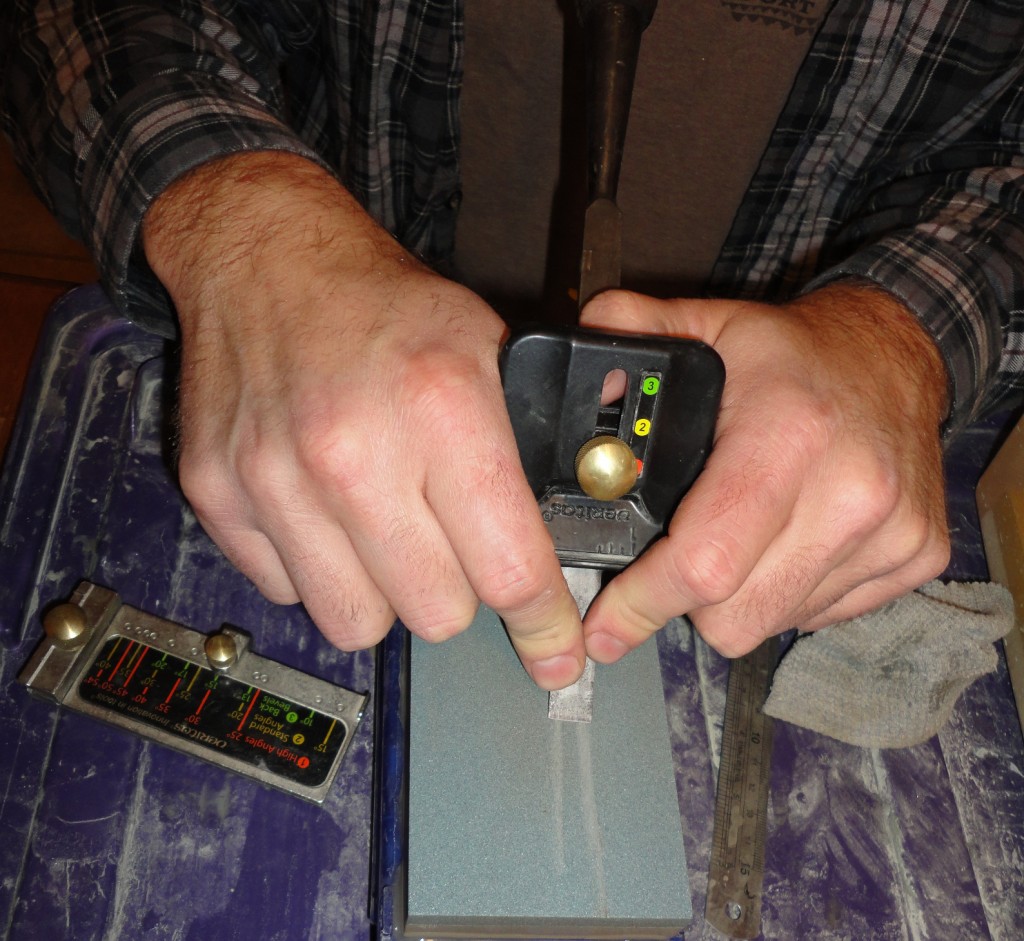
When I get to the 8000 grit stone, I set the sharpening jig up to add a micro-bevel. On this chisel, I alternated with polishing the micro-bevel and the back (with the chisel in the jig) a couple of times on the 8000 grit stone. I did this until I was satisfied that the entire edge was sharp.
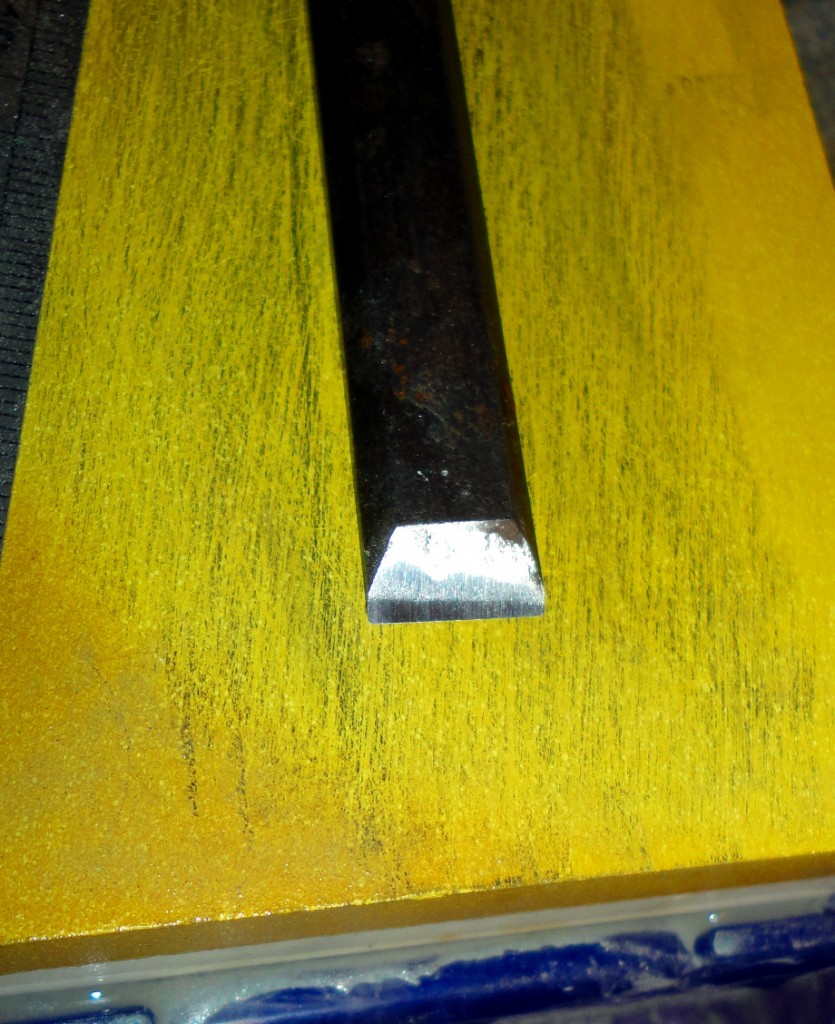